A Comprehensive Approach to Resolving Stretch Cover Maker Repair Difficulties
You recognize that stretch cover makers are important for keeping performance in product packaging operations. Issues can occur that disrupt performance. Recognizing usual troubles and carrying out preventive maintenance can greatly minimize downtime. And also, having trained operators can make all the difference in troubleshooting. What are the finest methods to guarantee your machines run efficiently? Let's check out the crucial elements of a detailed approach to deal with these repair service tests properly.
Comprehending Usual Stretch Wrap Device Issues
When you count on stretch wrap machines for efficient product packaging, it's vital to acknowledge common concerns that can interfere with operations - stretch wrap machine repair. One prevalent problem is irregular stress, which can result in inadequate covering and jeopardized load stability. If you discover the movie isn't sticking properly, check for damaged rollers or inappropriate settings
One more problem you might encounter is film damage, commonly brought on by incorrect movie kind or equipment breakdowns. Frequently check the machine for indicators of wear and tear to avoid this.
Additionally, watch on film build-up or jams, which can halt manufacturing. Often, this takes place due to misalignment or debris in the device.
Lastly, inappropriate sealing can result in tons coming apart during transit. Make particular your maker is calibrated correctly to maintain the honesty of your packages. By remaining attentive and addressing these issues promptly, you can promote smoother operations.
The Value of Routine Preventative Upkeep
Normal preventive upkeep is crucial for maintaining your stretch wrap device running smoothly and efficiently. By consistently inspecting and servicing your devices, you can find prospective issues before they rise right into costly repair work. This proactive strategy not only expands the life expectancy of your equipment yet additionally ensures that it operates at peak performance.
You must set up routine assessments to tidy, lubricate, and change worn parts. Maintaining your machine calibrated assists keep perfect covering high quality, reduces waste, and improves performance. Additionally, recording upkeep activities produces a trusted history that can inform future decisions.
Don't ignore the significance of training your personnel on upkeep best practices. When everybody recognizes how to care for the maker, you decrease the threat of operator error causing failures. Simply put, dedicating to regular preventative upkeep is a wise financial investment that pays off in minimized downtime and improved performance in your procedures.
Repairing Strategies for Quick Services
Efficient troubleshooting methods can significantly reduce downtime when your stretch wrap maker encounters issues. Is the equipment not wrapping correctly or is it making unusual sounds?
Following, inspect the machine's settings and controls; sometimes, a straightforward adjustment can deal with the problem. Inspect the film stress and placement, as incorrect arrangement can cause wrapping failings. Don't neglect electric connections; loose or broken cables can interfere with capability.
If you're still facing difficulties, think about running analysis tests if your device has that capability. Don't wait to consult with a specialist if you can not settle the issue rapidly.
Educating Operators for Effective Maker Use
To assure your stretch cover maker runs at peak performance, appropriate training for drivers is crucial. When drivers recognize the equipment's performances, they can maximize its possible and minimize downtime. Beginning by offering them with complete manuals that outline operational procedures and safety procedures. Hands-on training is vital; it enables drivers to acquaint themselves with the device's controls and settings.
Encourage them to practice under supervision, addressing any questions or problems they might have. Routinely scheduled correspondence course can keep their abilities sharp and help them adjust to any updates or changes in innovation.
In addition, instill a culture of liability by equipping drivers to report issues or recommend improvements. This positive method not only boosts their self-confidence however likewise contributes check my source to the overall efficiency of your operations. With trained drivers, you'll see less mistakes and increased productivity, guaranteeing your stretch cover device continues to be a useful possession.
Constructing a Strong Communication Network Between Teams
Well-trained drivers can just perform at their ideal when there's a solid interaction network between teams. Reliable communication gets rid of misconceptions and guarantees everybody's on the very same web page relating to device procedures and repair service needs. Motivate regular check-ins and conferences to discuss issues, share insights, and address worries.
Utilizing technology, like messaging apps or joint platforms, can boost real-time interaction, making it less complicated to report problems and share updates promptly. Designating clear roles and responsibilities fosters liability, allowing employee to connect to the appropriate person when look at here now problems develop.
Furthermore, creating an open setting where everyone feels comfortable sharing responses can cause ingenious solutions. By prioritizing interaction, you're not simply boosting maker performance; you're also developing a cohesive team that works together perfectly. This collective spirit eventually results in quicker repairs and decreased downtime, benefiting the entire procedure.
Purchasing Top Quality Replacement Parts
When it comes to keeping your stretch cover machines, purchasing top quality substitute components is crucial for guaranteeing reliable performance and decreasing downtime. Low-cost options might seem appealing, however they usually lead to more significant issues down the line, costing you a lot more out of commission and lost performance. By choosing premium parts, you're not simply taking care of a trouble; you're boosting the overall effectiveness of your equipment.
Additionally, high quality components are normally manufactured to stricter requirements, which implies they'll fit much better and work more accurately. This reduces the possibility of unexpected failures, permitting your operations to run efficiently. Reliable suppliers often provide service warranties, giving you peace of mind in your financial investment.

Evaluating Efficiency Information for Continual Renovation
To improve your stretch cover maker's efficiency, you need effective data collection strategies. By assessing efficiency metrics, you can identify locations for improvement and improve efficiency. Recognizing these opportunities not just enhances procedures however also reduces downtime and repair prices.
Information Collection Methods
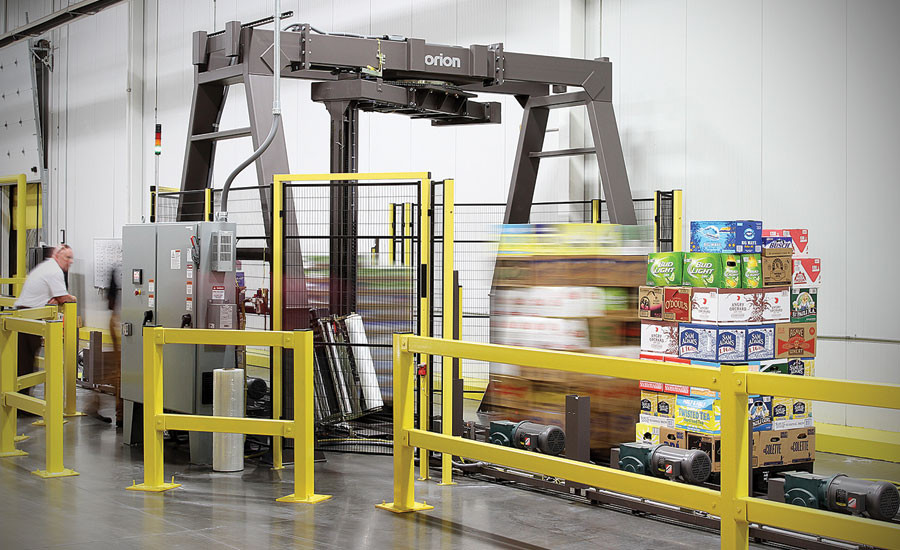
Performance Metrics Assessment
While assessing performance metrics, it's crucial to focus on specific information factors that straight affect your stretch wrap maker's efficiency. Start by tracking cycle times, as they disclose exactly how swiftly your equipment operates under regular problems. This continual evaluation assists improve performance, lower prices, and eventually boost your machine's long life, leading to an extra effective covering procedure generally.
Identifying Improvement Opportunities
As you evaluate efficiency information, you can reveal useful improvement opportunities that boost your stretch wrap equipment's efficiency. Look for trends in downtime, cycle times, and wrap quality. If frequent malfunctions associate with particular operating conditions, you can change processes to reduce these concerns.
Often Asked Questions
Just How Can I Inform if My Machine Demands a Repair Service or Simply Maintenance?
To inform if your machine requires repair service or just maintenance, listen for unusual noises, look for irregular performance, and check for visible wear. If issues linger after maintenance, it's most likely time for a repair.

What Is the Average Life-span of a Stretch Wrap Maker?
The average lifespan of a stretch wrap machine is commonly 5 to ten years, relying on usage and maintenance. Regular care can prolong its life, so watch on performance and address concerns without delay.
Are There Certain Brand Names Understood for Better Integrity?
Yes, some brands are known for their reliability. You'll discover that firms like Signode and Lantech often obtain favorable evaluations - stretch wrap machine repair. Looking into user comments can help you choose a trustworthy stretch wrap equipment for your demands
What Are the Signs of Poor Operator Training?
If you observe constant errors, irregular wrapping, or safety and security cases, those are signs of inadequate driver training. Absence of recognizing concerning maker functions or failing to comply with protocols can significantly influence performance and security.
Just How Can I Find a Certified Technician for Repair Works?
To locate a qualified technician for repairs, ask for recommendations from industry peers, examine online evaluations, and confirm certifications. You could additionally consider contacting regional devices vendors that frequently have actually trusted technicians available.
Conclusion
To sum up, tackling stretch wrap device repair service challenges requires an aggressive method. Don't neglect the importance of strong interaction between groups and continual assessment of maker output.